Carbon Dioxide Transport and Storage
Summary
US-REGEN explicitly models the transport and storage of captured CO2 on a regional basis. Carbon can be captured in a wide range of applications, including power plants, fuel conversion plants, certain industrial plants, and direct air capture plants. For long-term geologic storage, the captured CO2 can be transported to injection sites and stored underground reservoirs, such as saline aquifers. The costs for transport and storage of captured carbon include investments in both pipeline capacity and CO2 injection capacity, as well as ongoing operating and maintenance costs. Regional storage capacity is limited based on estimates from the National Carbon Sequestration Database (NATCARB).[1] However, investments in inter-regional CO2 pipeline capacity can be made to access capacity in neighboring regions. Additionally, intra-regional pipeline capacity is needed to connect capture sources (e.g. power plants) with injection sites.
CO2 Storage Costs and Capacity
The capital costs for CO2 injection capacity are derived from gridded geologic data in NATCARB, taking into account well drilling and surface equipment requirements as a function of formation depth, thickness, porosity, and pressure, as shown in in Figure 1. The gridded data is aggregated into state- and region-level average costs for use in REGEN. State-level average capital costs vary significantly, from approximately $10 per tCO2/year injection capacity in the most favorable regions to $30-$50 per tCO2/year in less favorable regions. On a levelized basis, this translates to a cost range of roughly $1-$5 per tCO2 stored. Figure 2 shows the available capacity for cumulative storage of CO2 by state and aggregate model regions. Note that 14 states have effectively zero CO2 injection potential and thus rely on pipeline transport for carbon capture and storage applications.
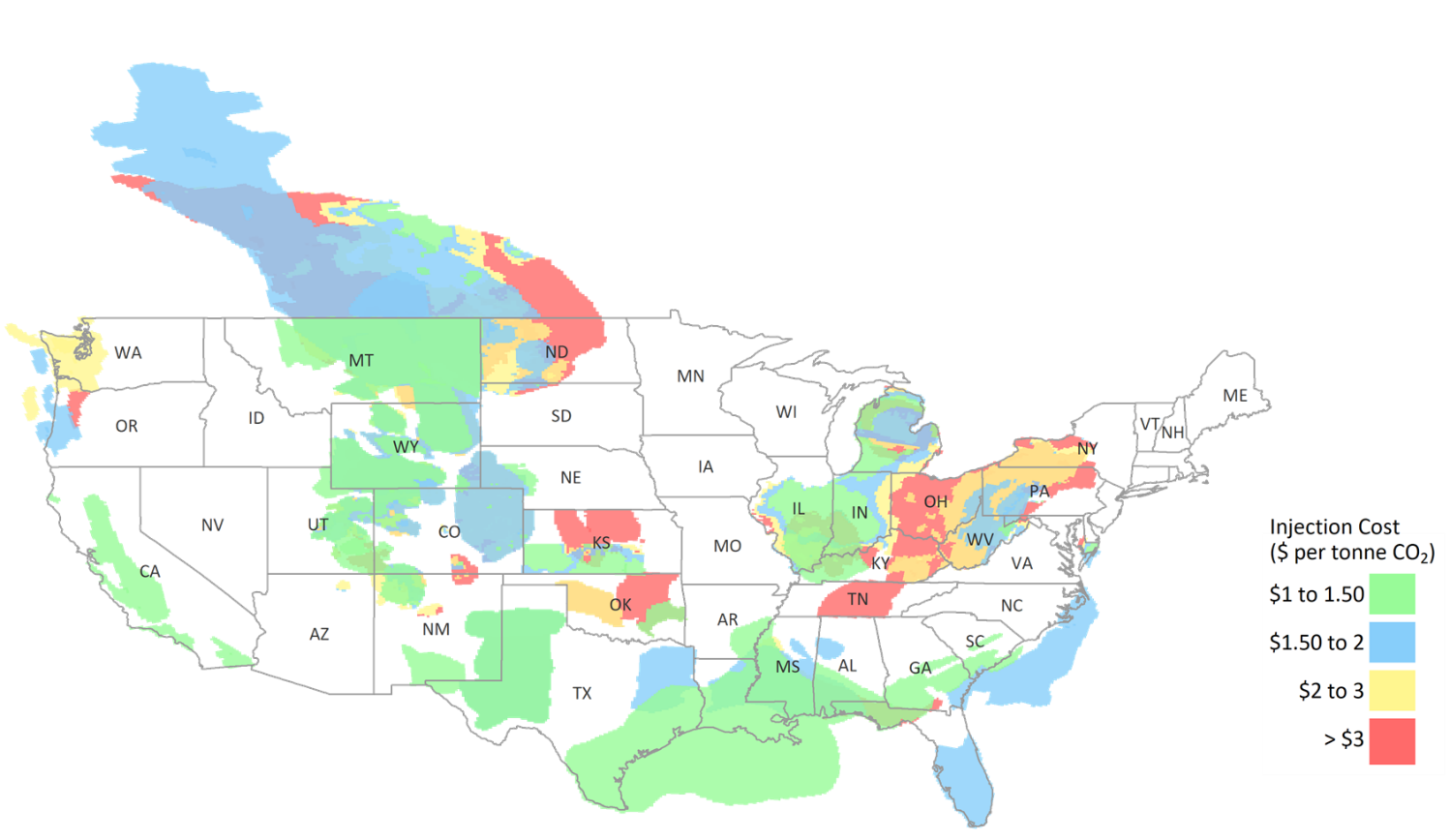
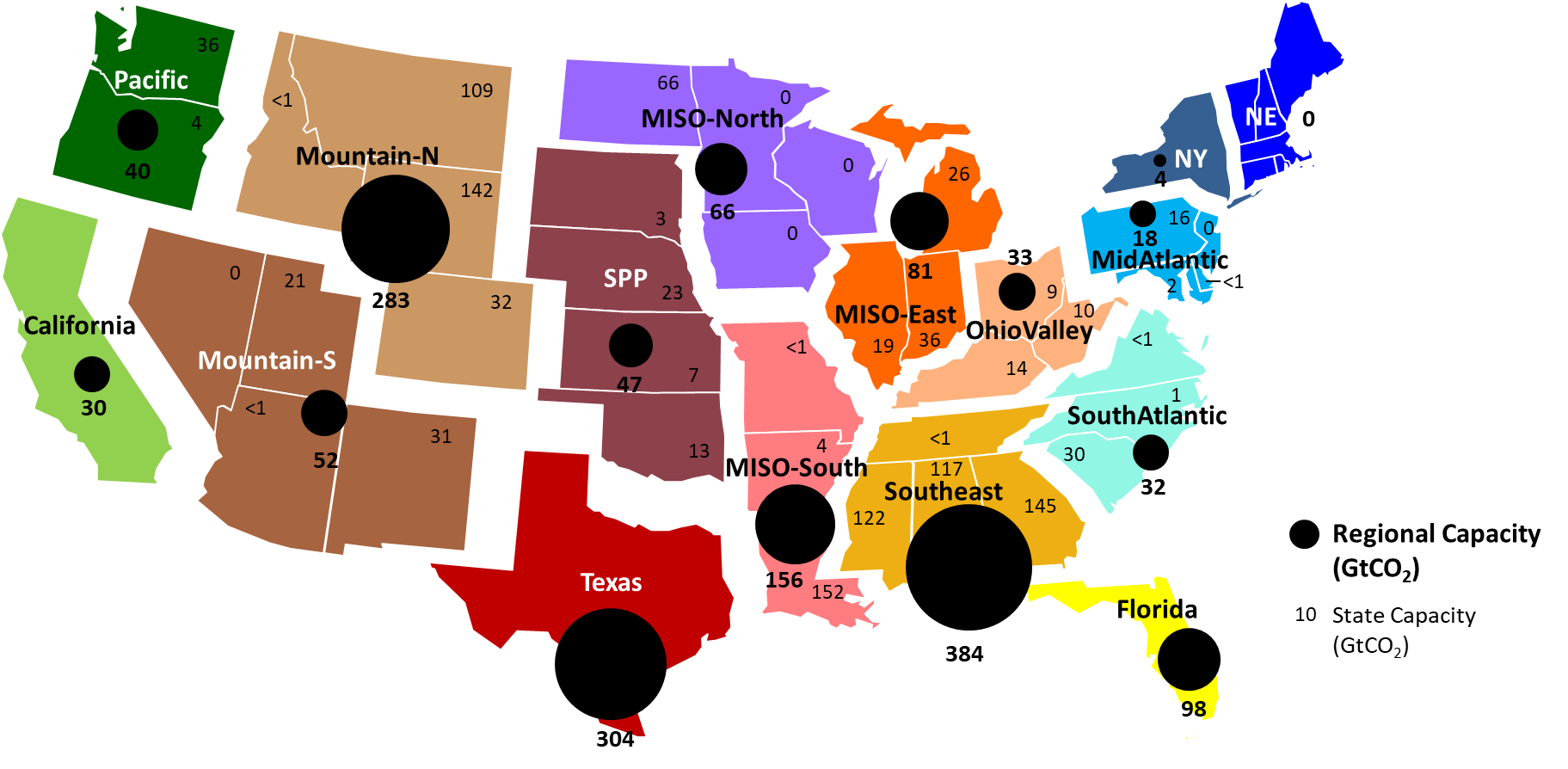
In addition to the capital costs, REGEN includes an annual fixed operating cost term associated with maintaining the injection site and managing the operational issues arising from injected CO2 flows, including brine removal and periodic testing for seismic and other impacts. These annual costs are assumed to be 15% of the initial investment cost, which implies they are a larger component of total levelized cost of storage than annualized upfront investment cost. The injection site must also be monitored and maintained into the future after the end of its active life. The net present value of these costs is estimated to be roughly 10% of annual operating costs during the injection period. This results in a total levelized cost of CO2 storage of $3-$15 per tCO2. EPRI is conducting further research under LCRI to characterize injection capital and carrying costs in greater detail.
CO2 Transport Costs
REGEN represents CO2 transport costs via pipeline at two levels, similar to other commodities: inter-regional CO2 transport, for example to move captured CO2 from a region with limited or no injection capacity to another region with better injection potential; and intra-regional CO2 transport to connect sources of CO2 capture with injection sites within a region. For inter-regional transport, pipeline capacity investments costs are based on a 42-inch diameter pipeline with 20% average utilization (a relatively conservative assumption, higher utilization would lead to lower costs), scaled by the distance between region centroids. For intra-regional CO2 transport, each capture application includes a scaled pipeline investment component based on assumed flow rate and distance between capture plant and potential injection site. For carbon capture retrofits of existing power plants and new bioenergy plants with capture, siting near injection capacity will be more difficult (i.e. driven by the existing plant's location or the biomass feedstock source), thus REGEN assumes longer pipeline distances for these applications, which are assumed to be met through a hypothetical network combining feeder and trunk lines. For new gas-fired power generation and hydrogen or ammonia production, or for direct air capture, REGEN assumes siting could be more easily dictated by a suitable injection location and thus would entail shorter pipeline distances, essentially feeder only. Figure 3 summarizes the pipeline scale assumptions and associated costs for each CO2 capture application. Figure 4 summarizes the assumed capital costs and CO2 nominal flow rate for different pipeline sizes. Both inter-regional and intra-regional pipeline capacity also has an annual carrying cost (i.e. fixed operating and maintenance) estimated at 2.5% of capital costs.
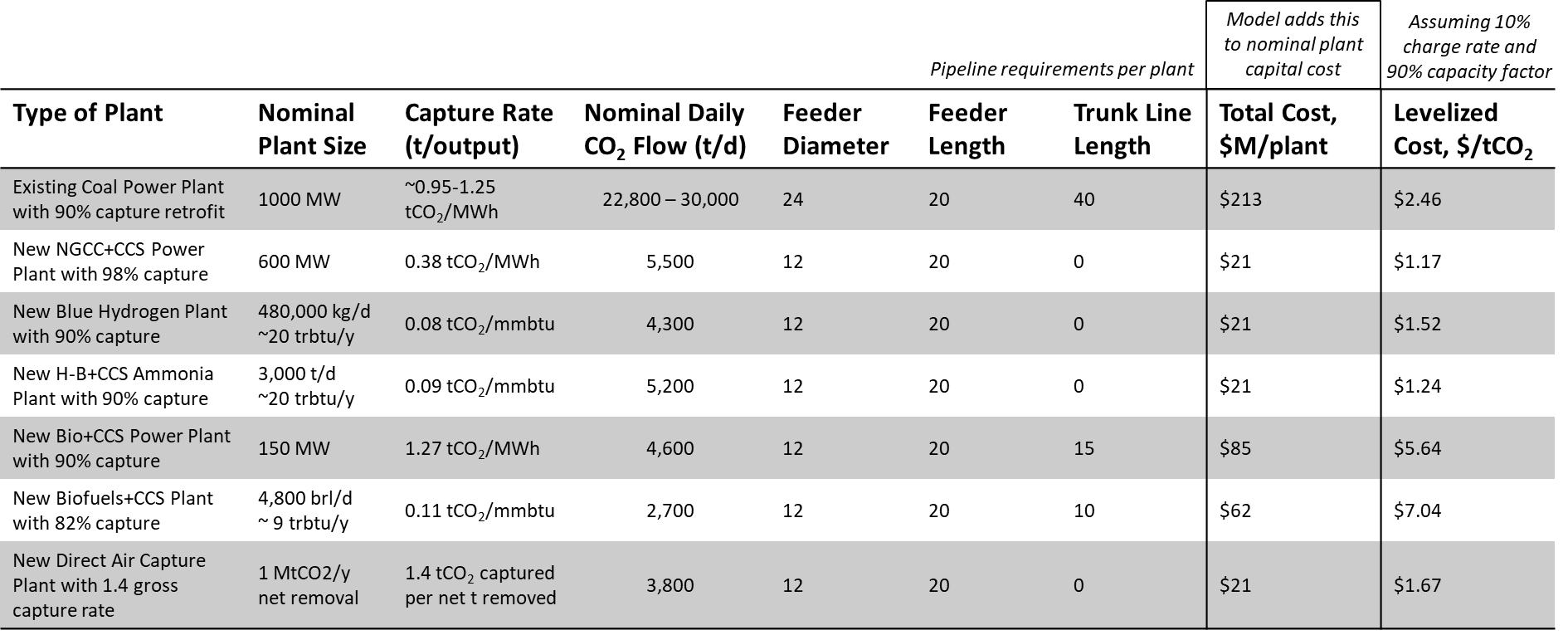
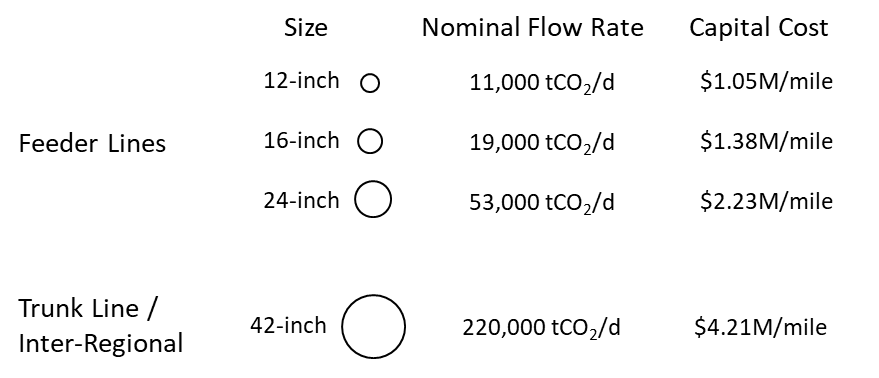
Note that there are economies of scale with pipeline transport, i.e. the levelized cost of transport declines with increasing flow. Moreover, there is significant spatial variation both within and across regions in terms of alignment between capture plant and injection sites. The current US-REGEN estimates reflect representative average levelized costs, whereas actual transport costs for individual projects could vary considerably. EPRI is conducting further research under the Low-Carbon Resources Initiative to characterize CO2 transport requirements and costs in greater detail.
National Carbon Sequestration Database (NATCARB), v.1502. https://www.netl.doe.gov/research/coal/carbon-storage/natcarb-atlas ↩︎